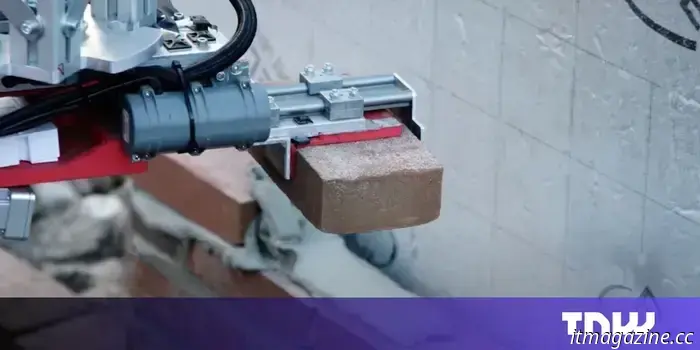
Can construction robots address Europe’s housing crisis?
Europe's housing crisis is intensifying. High construction costs, stringent regulations, and labor shortages have severely restricted the availability of affordable housing. As cities grow with increasing populations and a mass retirement of construction workers, the gap between supply and demand continues to expand.
Numerous solutions have been suggested. Large housing projects, reworking the planning system, modular construction, prefabricated materials, rent control measures, and limits on corporate home purchases have all been considered, but the deficit of affordable housing persists.
Dutch startup Monumental has proposed an additional solution: automation. The company is developing a range of autonomous, electric robots designed to operate continuously on construction sites.
Salar al Khafaji, CEO and co-founder of the startup, believes this technology can address the labor, cost, and regulatory challenges plaguing the industry. “It’s clear that automation and robotics are needed to tackle these issues,” he states. “There’s hardly any alternative.”
During the TNW Conference in Amsterdam on June 19-20, al Khafaji will share insights on building a successful robotics business. Leading up to his presentation, he discussed his vision for the future of construction.
The stagnation in construction
Before founding Monumental in 2021, al Khafaji co-founded a visualization startup named Silk. After Silk was acquired by US analytics company Palantir in 2016, he began considering his next venture. His intention was to tackle a significant global issue. “I wanted to address a serious societal problem,” he says. “And I became fascinated with construction and infrastructure.”
Al Khafaji was taken aback by the limited technological advancements in the sector, which severely impacted the built environment. He concentrated on a key issue: the productivity decline in construction. He feared that labor shortages, stringent regulations, and high costs were exacerbating the housing crisis. New developments were becoming extraordinarily costly and frustratingly slow to finish, often resulting in unpopular designs.
Historically, comparisons are not favorable. The Empire State Building, for example, was completed in just 410 days in 1931, while 432 Park Avenue, finished 84 years later, took 1,500 days and became notorious for issues like leaks and malfunctions alongside a divisive architecture.
This problem extends beyond iconic structures. The construction of typical homes has also slowed down. The average time required to build a single-family house rose from 4.8 months in 1971 to seven months in 2019. Even when adjusting for the increase in average house size, the process is still slower today.
Longer construction timelines result in higher costs, with labor often being the primary expense. “It’s extremely labor-intensive because we’ve hardly automated anything there,” al Khafaji observes.
Monumental aims to change the current paradigm.
Addressing the housing issue
Al Khafaji co-founded Monumental in 2021 with his long-time business associate, Sebastiaan Visser, who serves as the company’s CTO. Their primary concept involved automating on-site construction with robots and software. They began with a prototype robotic crane, which evolved into autonomous ground vehicles designed to transport building materials around construction sites.
The first completed system focused on one essential construction task: bricklaying. This was a logical starting point. Bricklaying is a skilled, physically demanding, and sometimes hazardous occupation experiencing a significant decline in workforce. In 2022, research indicated that 19 European nations faced a shortage of bricklayers, making it the profession with the largest labor shortfall. This scarcity leads to delays and increased costs in construction projects.
With the profession struggling to attract younger workers, the shortage is expected to worsen. In the UK, the number of bricklayers recently reached a 25-year low, with a third expected to retire within the next decade.
Monumental’s systems are designed to bridge this gap and ultimately enhance the availability of affordable housing. The startup’s electric bricklaying robots operate autonomously alongside human workers, using sensors, computer vision, and small cranes to accurately place bricks and mortar in walls. The system is also designed to work within existing construction processes, which is vital in an industry that is not always receptive to new technologies.
The robot builders
Al Khafaji likens the robots to distributed computers. Each robot consists of multiple interconnected modular components, functioning like network devices. To prepare the machines for construction tasks, the startup’s software models both the construction site and the robots themselves. A machine vision stack enables them to navigate the building area, while AI manages their operations.
“We consider it an operating system for construction sites,” al Khafaji states. “We’re working to make construction more software-defined.”
In 2023, the robots completed their first large-scale, 15-meter wall. Since then, they have constructed facades for houses, retaining walls along canals, and other structures currently found throughout the Netherlands. Investors have been impressed with their progress; last year

Other articles
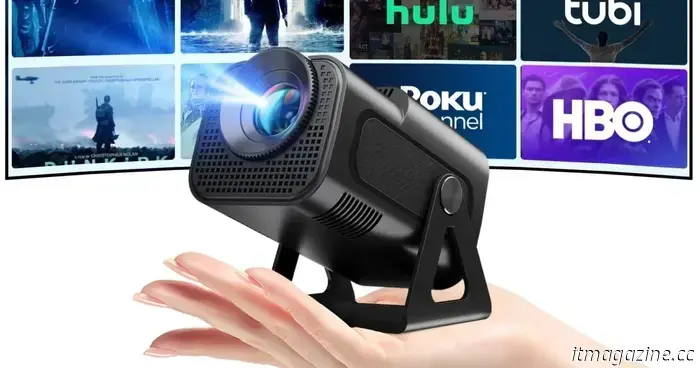
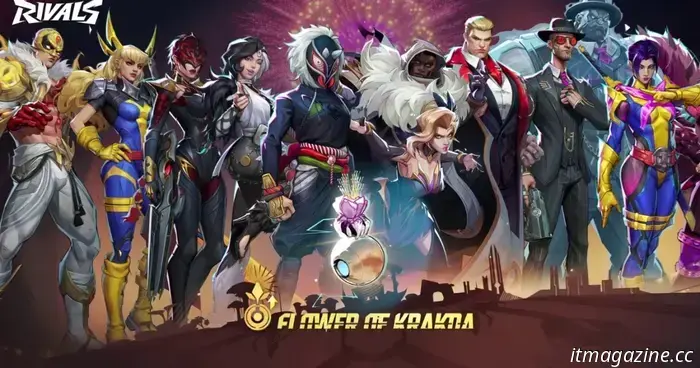
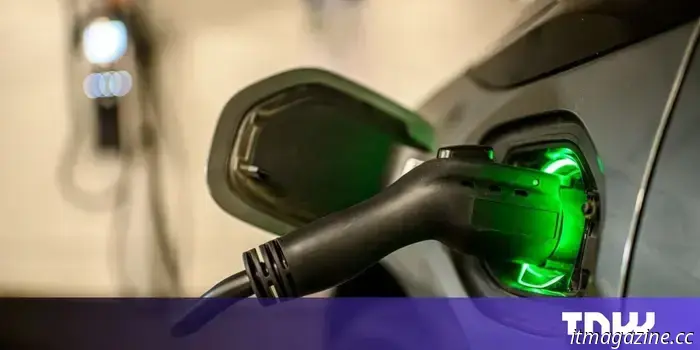
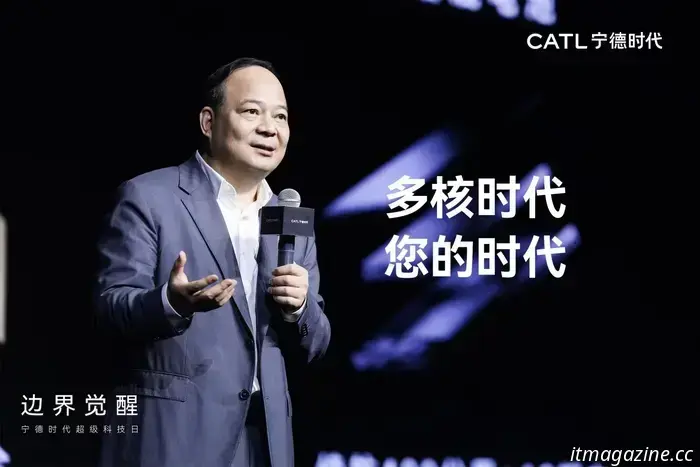
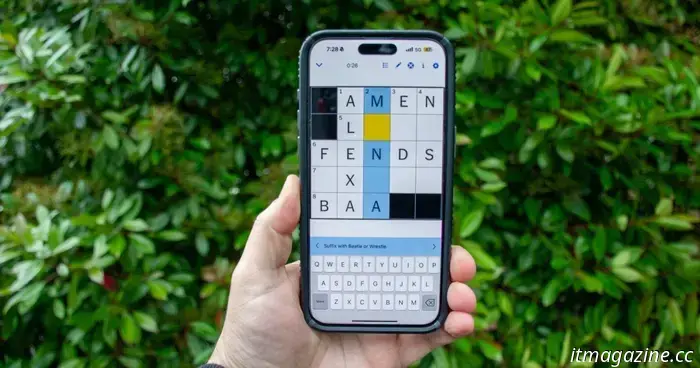
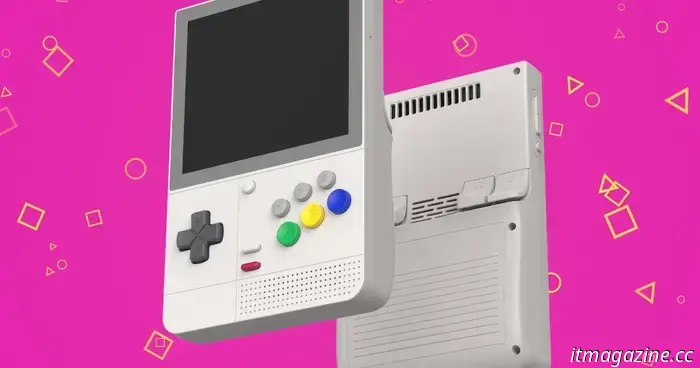
Can construction robots address Europe’s housing crisis?
Monumental CEO Salar al Khafaji, who spoke at this summer's TNW Conference, thinks that robotics are essential for alleviating the housing crisis.